Enhancing Plant Reliability Through Redlist
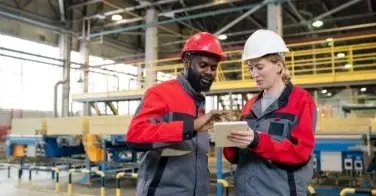
At a leading corrugated paper manufacturing company, ensuring consistent and reliable plant operations is paramount. The role of Area Reliability Director, held by Dewayne F., involves overseeing the maintenance and reliability across multiple plants. The management team faced several challenges, particularly in the lubrication program—a critical aspect of plant maintenance that directly impacts equipment uptime and reliability.
The Challenge:
Before the integration of Redlist, the management team grappled with inefficiencies in maintenance routines. Lubrication tasks were time-consuming, and their completion was hard to verify, leading to prolonged downtimes and reactive maintenance strategies. Additionally, accountability was difficult to enforce, often resulting in the proverbial finger-pointing when equipment failed, posing the question, “Did it get lubricated?”
Overcoming Resistance:
Implementing new technology often meets resistance, and Redlist’s Proof of Presence feature was no exception. Dewayne reassured his team that the feature was not about a lack of trust but about providing clear evidence of task completion. “It’s really easy for my guys to prove that they did their job,” he explains, highlighting how Redlist bolstered both accountability and assurance within the team.
Consistency in Lubrication and Reliability:
Dewayne shared with his colleagues the critical importance of a tool like Redlist, stating, “without a tool like Redlist, that manages the lubrication program down to the point, that has proof of presence and the ability to easily audit the process, your lubrication programs are not going to be as consistent as they need to be. If your lubrication is not consistent, then reliability is not going to be consistent either.” The case for Redlist was clear—it provided the structure and precision necessary for a solid lubrication program.
Impactful Results:
Redlist was introduced to address these challenges head-on. Dewayne recounts, “One of my favorite things about Redlist is it allows me to easily audit my plants and their lubrication process.” The ability to walk onto the floor, scan a QR code, and instantly access lubrication and inspection history revolutionized the way maintenance tasks were verified and recorded.
The most telling impact of Redlist was the dramatic reduction in time required to complete maintenance routes. “It used to take our team 6 to 8 hours to complete a route with two people,” Dewayne recalls. With Redlist, routes were completed in half the time, allowing the team to direct their efforts to other projects, thereby improving overall efficiency.
Collaboration and Continuous Improvement:
Dewayne emphasizes the collaborative nature of Redlist, saying, “Redlist has been great to collaborate with.” The open exchange of information allowed for the tool and the company’s maintenance program to evolve together, ensuring the solution was finely tuned to the plant’s specific needs.
Conclusion:
Dewayne’s leadership in deploying Redlist has revolutionized maintenance operations. By enhancing lubrication processes and introducing a culture of accountability with the Proof of Presence feature, maintenance times have been halved, allowing teams to prioritize other critical tasks. This shift has not only improved efficiency but also established a new industry standard for operational excellence.