How to Simplify Your Lubrication Management Routes?
- Redlist
- May 6, 2024
- 4 min read
Updated: Aug 6, 2024
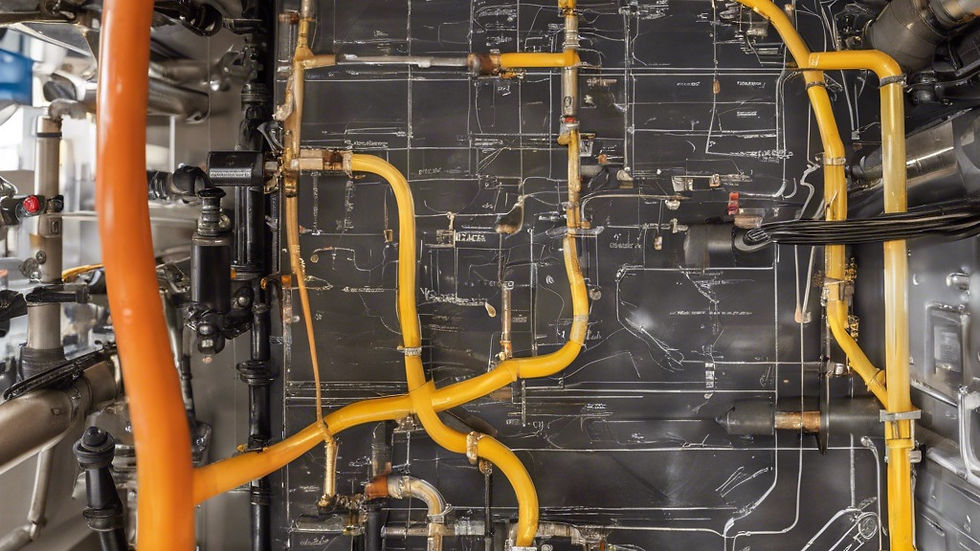
To some, lubrication management routes are simply a list of machines or equipment to be greased or oiled on schedule. For effective lubrication, however, lubrication routes must accomplish a complex set of steps and processes.
Simplifying these steps will make them easier to implement, thus achieving effective lubrication, improving the bottom line, and increasing asset reliability.
In this post, we will help you gain a better understanding of the complexity of establishing and implementing lubrication management routes. Furthermore, we will also investigate the valuable ways of simplifying this process, which include the use of modern tools like Redlist.
What are Lubrication Management Routes?
Lubrication management routes are a set of planned or scheduled lubrication activities that maintenance team members must execute to ensure optimum lubrication, smooth operations, and asset longevity.
These route activities are not only limited to lubricant application, but also include:
Inspection for early signs of wear and tear
Monitoring lubricant levels and replacement as needed
Cleaning the areas of lubrication
Checking the integrity of seals and fitting
Documenting maintenance and lubrication activities for future reference
Aside from details on the activities or tasks mentioned above, lubrication management routes must also contain the following information:
Specific machine or equipment that requires the route task or tasks
Frequency or how often to perform said tasks
Technicians or personnel responsible for completing or supervising routes
Necessary tools, materials, and equipment
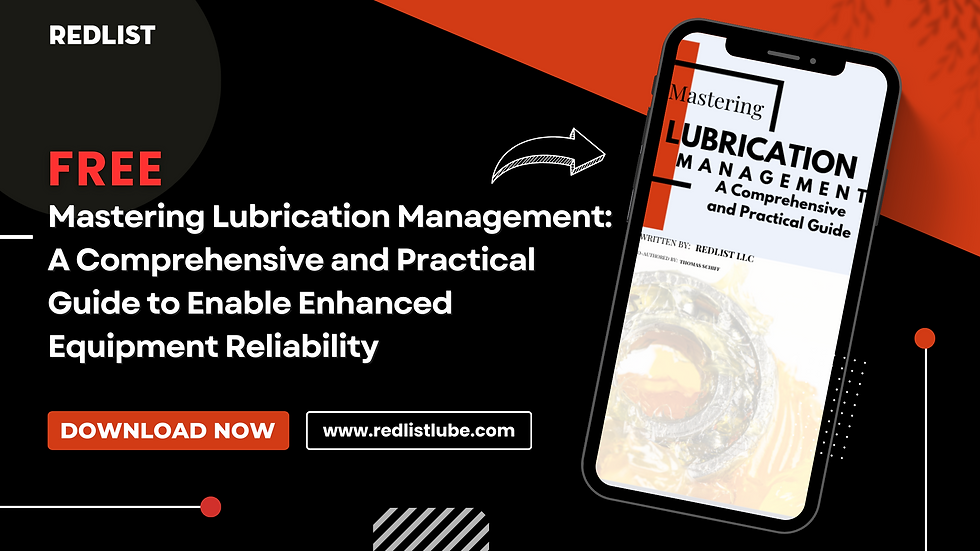
4 Ways in Simplifying Lubrication Management Routes
With many things to consider, creating lubrication management routes can feel complicated and overwhelming. The following are the most valuable ways of simplifying your routes and achieving optimum lubrication results:
1. Task Plans
As with any endeavor, planning is critical for success. When it comes to lubrication management routes, creating task plans means understanding what you need to do and how often.
Task plans help promote standard procedures and prevent confusion, inefficiency, and redundancy.
Effective task plans must include all the necessary details and instructions, but still be easy to read and follow. Task plans require being routinely reviewed and updated as the lubrication and maintenance needs of every asset change over time.
2. Monitoring Tools & Practices
Modern lubrication tools and practices are available that can simplify and improve lubrication processes. Machines can now be equipped with sensors that connect to devices that monitor the lubricant conditions.
These tools allow faster and more accurate inspections without the need to shut down or dismantle machines.
To get the best out of these tools and practices, the data that they provide must be collected and stored properly. That way, the data can provide accurate insights that are critical for evaluating and improving current lubrication strategies.
3. Technical Training & Certifications
The successful completion of lubrication management routes depends on the expertise of the technician or personnel executing the route tasks. Thus, creating an effective training and certification program is critical.
Technicians or any personnel involved must be trained in how to correctly perform lubrication and other tasks involved.
Any person you assign to execute lubrication tasks must be knowledgeable of standard lubrication procedures and other maintenance processes like requesting tools or materials, completing reports, submitting recommendations, etc.
Additional tasks can also require special certifications like oil analysis and lubricant application.
4. Feedback & Communication
Finally, an effective system that allows fast feedback and clear communication can also simplify lubrication management routes. Feedback is necessary to collect the data for critical improvements.
Sharing and distributing essential lubrication information also allows for collaborative work between team members.
Feedback from lubrication tasks must be recorded and stored securely to be accessed when needed. Critical feedback that needs immediate action must be issued in real-time to prevent delays and reduce downtime.
Redlist Simplifies Lubrication Management Routes
Redlist is one of the most in-demand Lubrication Management Software options today. It comes with the following benefits that make Redlist indispensable if you seek to make your lubrication management routes simple yet effective:
Professional Program Support – Redlist’s team of lubrication experts can chart your facility on-site and evaluate your current lubrication routes and practices. From the data gathered, we can then help you design the ideal lubrication program based on your current needs.
User-Friendly and Time-Saving – Redlist’s intuitive interface, simplified workflow, and automated functionalities allow for faster completion of tasks and reporting. Redlist also works on both mobile and desktop devices, allowing mobile connectivity and minimizing feedback or information delays.
Real-Time Updates – Redlist lets you issue updates, notifications, or alerts on any maintenance tasks. This functionality is helpful for critical tasks that need immediate feedback. Other benefits include updating inventory levels and sharing information among maintenance team members and other departments.
Powerful Analytics – Redlist lets you get actionable analytics from any information you collect, thus driving continuous lubrication improvement.
Lubrication Management Routes Case Study
To further understand how Redlist helps with lubrication management routes, it is worth sharing the result of a Redlist client case study that involves a sustainable wood company.
Before Redlist, the company lacked any lubrication plan and was incurring major losses in bearing replacements, repairs, and downtime.
Upon installing Redlist’s Lubrication Management Software, the company set out to create a lubrication strategy. To do that, the company had to chart its assets, components, and lubrication.
It is a tall order, but with the help of Redlist’s expert engineers and technicians, they were able to chart 500 assets, 1,200 components, and 2,300 tasks in only four days. Soon after charting was done, routes were easily assigned.
The Redlist users were then given access to the software for recording and reporting data.
The impact of Redlist on the company was 100% completion of lubrication management routes. That is a huge leap from having no lubrication program and no documented lubrication routes at the beginning.
After a year of following the lubrication program with Redlist, the company only had one bearing failure, and that was not even due to a lubrication issue.
The increased reliability resulted in $300,000 worth of savings in downtime costs and an estimated savings of $180,000 per year on labor costs because they did not need to hire additional personnel for lubrication tasks.
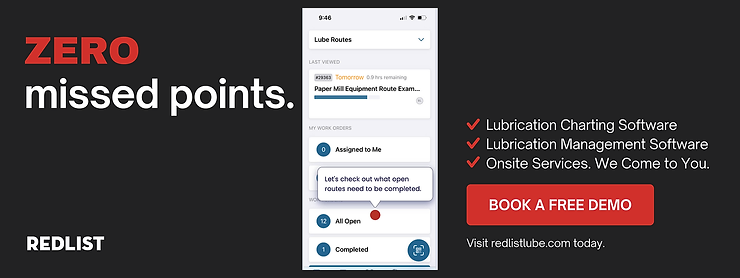
Let Redlist create or simplify your lubrication program today. Request your free Redlist lubrication management demo with our experts to experience similar benefits for your facility.
Comments