The Risks and Consequences of Bearing Failure Caused by Over-Lubrication
- Redlist
- Jun 17, 2024
- 4 min read
Updated: Aug 6, 2024
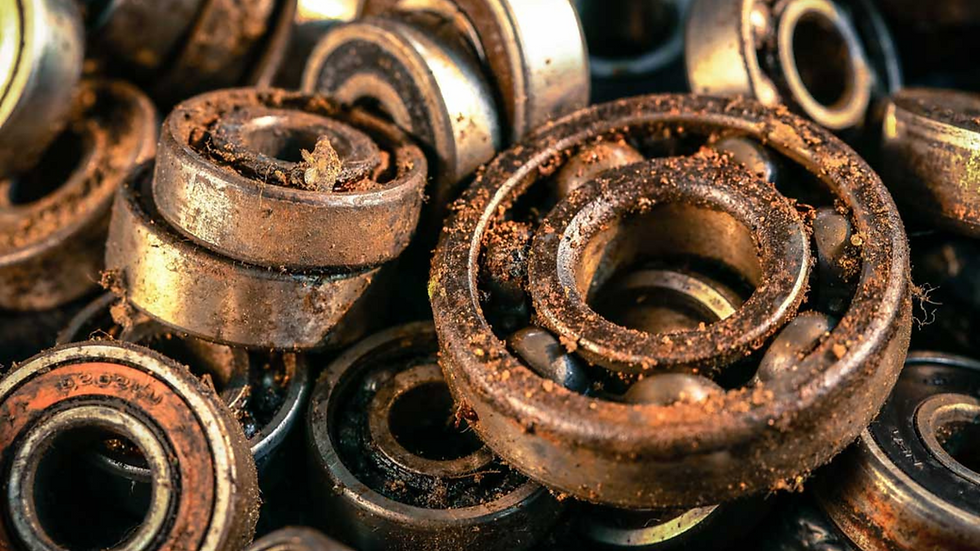
Lubrication is critical for efficient, long-lasting, and productive machines and assets. But you know what they say about having too much of a good thing. Too much lubrication can adversely affect machine parts, particularly the bearings. With a proper understanding and implementation of lubrication practices, you can prevent and mitigate the risks and consequences of over-lubrication.
Lubrication and Bearings
First, let’s understand how lubrication works on bearings. In machines, bearings are parts or systems of parts that allow or assist a machine’s rotation and other movements. Applying lubricants on machine bearings:
Reduces friction by creating a film between metal surfaces, thus minimizing metal-to-metal contact and making movement smoother and more efficient.
Dissipates heat by absorbing and carrying it away from machine parts as it flows, preventing overheating and chemical reactions that threaten the integrity of the bearings.
Reduces wear and tear by preventing abrasion between in-contact surfaces, prolonging the lifespan of the bearings and the entire machine.
Protects bearings by forming a barrier against dust and other contaminants that cause damage and corrosion.
Bearing Failure Due to Over-Lubrication
Applying too much lubricant can lead to bearing failure in the following ways:
1. Increased Friction
Excess lubricant can increase internal friction within the bearing. This increased friction generates heat and degrades lubricant and bearing materials.
2. Heat Generation
Excess lubricant results in heat generation and higher operating temperatures in bearings. These high temperatures promote the faster breakdown of lubricants, increasing the need for frequent re-lubrication.
3. Seal Damage
Excess lubricant can also result in an increase in pressure within the bearing. Seals can collapse or break at certain high-pressure levels, allowing contaminants to enter and lubricant to leak out of bearings.
4. Increased Drag
Excess lubricant increases the drag on the bearing. This increased drag leads to higher energy consumption, and thus, reduces the efficiency of machines. Increased drag also causes too much fatigue on bearing components, leading to shorter bearing lifespan, frequent bearing failure, and constant machine breakdown.
5. Grease Churning
Excess lubricant can be churned out by the rotating bearing components and pushed out of the bearing housing. This churning results in oil degradation and oil bleed, or separation of oil and thickener. Churning can also result in lubricant leakage that can contaminate other machines and cause other housekeeping issues.
Risk and Consequences of Bearing Failure from Over-Lubrication
If uncontrolled, bearing failures due to over-lubrication can result in the following risks and consequences:
High Operating Costs
Bearing failures from over-lubrication reduce bearing life and increase the need to replace the bearing. Frequent parts replacements and operation disruptions all lead to high costs of operations.
High Maintenance Costs
Bearing failures from over-lubrication increases maintenance workload with activities like cleaning excess grease, replacing damaged seals, reapplying leaking lubricants, and many more. Naturally, more maintenance workload means more costs in terms of spare parts, materials, personnel, and other resources.
Low Efficiency
Bearing failures from over-lubrication makes machines less efficient by increasing drag and energy consumption. Low-efficiency machines contribute greatly to high energy costs and low overall productivity.
High Environmental and Safety Risks
Bearing failures from over-lubrication also increases safety risks and environmental impact. Oil leakage, for example, poses a risk of slipping accidents. This leakage can also result in environmental contamination, causing regulatory fines and clean-up costs for the company.
Dealing with Bearing Failure Due to Over-Lubrication
Prevention is the best way of dealing with bearing failures from over-lubrication. You can prevent over-lubrication by:
Following the manufacturer’s recommendations. Machine manufacturers know the right amount and frequency of lubrication that their machines need. Exceeding the recommended amount and frequency is not advisable and can only lead to over-lubrication and its damaging effects.
Implementing proper maintenance practices. Train all relevant lubrication personnel on the proper application of lubricants. Using standard and regularly calibrated oil dispensing tools can further ensure that the correct amounts of lubricants are applied.
Performing regular monitoring and maintenance. Routine checking, monitoring, and early preventive maintenance all help prevent over-lubrication. Signs like excess grease, high bearing temperatures, and irregular or abnormal vibration can be monitored to detect and deal with over-lubrication early.
Using automated lubrication systems. You can now use automated lubrication systems to ensure that the correct lubricant amount is dispensed at regular intervals. These systems help achieve optimal lubrication with minimal human error. However, these systems still need to be calibrated and monitored regularly for the best results.
Redlist for Over-Lubrication Control
A Lubrication Management Software (LMS) like Redlist can be the best tool when dealing with over-lubrication and its damaging effects. Redlist helps prevent bearing failure due to over-lubrication by:
Precise scheduling - Redlist allows you to automate lubrication schedules based on the specific needs of a machine. You can also adjust and customize these schedules depending on the changing requirements of your machines or other assets.
Data recording and analysis - Redlist helps you keep a record of lubrication data such as the amount of lubrication applied over time. These data help you make informed decisions when improving or enhancing lubrication practices.
Real-time condition-based monitoring - Redlist can integrate with lubrication monitoring devices for real-time data on lubrication conditions. This helps you identify over-lubrication before it happens or escalates into significant issues.
Alerts and notifications - Redlist can generate alerts when lubrication frequency reaches beyond a set limit. It can also issue notifications for upcoming lubrication schedules with details on proper amounts and correct application procedures.
Redlist leverages modern technology to help control over-lubrication and other lubrication management issues. Experience Redlist and its valuable benefits: Schedule a free demo with our experts today!
Comentarios